Boat:
Rhumb Do Date: August
2020
My steering system appears to be bombproof with substantial joints and
1" diameter tubes throughout, so apart from applying grease to the two
nipples on the tie rod ends, I have done very little to it - big
mistake!!
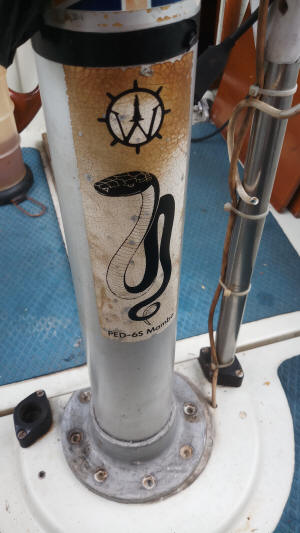
The boat is fitted with a Whitlock Mamba steering pedestal which is
connected to the rudder quadrant via torque tubes which are converted
to linear movement at the final transfer/reduction gearbox. The
"ultimate" steering system according to Lewmar!
The
pedestal is a PED-6S model from when Noah was a boy and there are
neither drawings nor parts available anymore, which is problematic when
you have a total steering failure as you come in to anchor in a small
'pond!'
We had just completed a 180NM trip from Labuan
to Kudat around the northern tip of Borneo and were entering the pond
when there was a graunching noise from the pedestal and all steering
ability went out of the window.
My preliminary
inspection revealed that the output shaft from the bevel gearbox
immediately under the deck at the base of the pedestal, was not
responding to any wheel movement.
.jpg)
Universal joint connects the bevelhead gearbox output shaft
to the torque tubes.
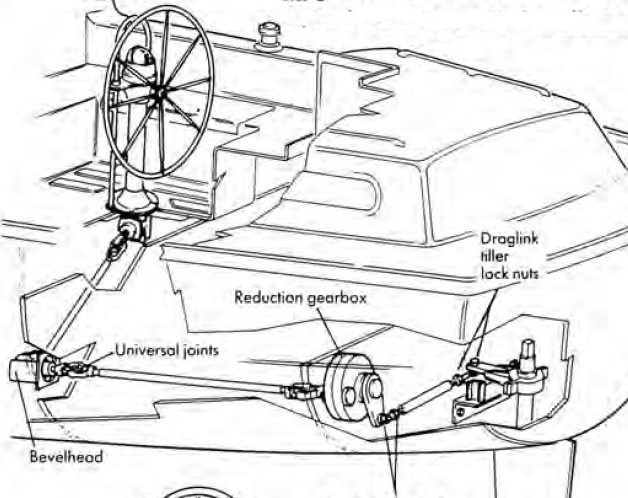
The above drawing shows a similar set up to mine.
On mine the torque tube comes from the bevelhead gearbox at the base of
the pedestal directly to the reduction/transfer gearbox, where the
rotary movement is converted to linear movement and then via a long
torque tube to the rudder head. On this tube are ball joints/tie
rod ends/drag links at each end (depends where you are from as to the
name!)
When I started to strip down the system, it was obvious
that someone else had done a few repairs or modifications in the past,
and advice from fellow Warrior owners did not fit with what I was
actually seeing and experiencing.
.jpg)
This is the bevelhead gearbox stripped down. The
arrowed male splines are worn away as are the matching female splines on
the pedestal downshaft. The two roller bearings and the two needle
bearings are also worn. The two oil seals were leaking.
.jpg)
The pedestal bowl with the compass and top plate removed.
The shaft you can see is the steering wheel input shaft. To the
right is the bearing carrier housing, to the left is the shaft end bush.
.jpg)
The same view with most of the grease removed, the
bearing carrier removed and both the steering input shaft and the
pedestal downshaft withdrawn. Withdrawal of the pedestal downshaft
(according to Whitlock) has to be done from the top - but that is
impossible because the (modified) female splined fitting at the bottom of the shaft
will not pass through the bearing! At the top of the shaft are two
roller bearings, in the pic, the upper one has been removed, the lower
one is still in place. The lower bearing carrier is secured to the
bowl by the four visible studs and nuts, which means you would need a
40" long extension bar to undo them from the bottom of the pedestal,
that's if there was room between the nuts and the side of the pedestal
in which to fit a socket - which there is not! In my case, the
lower bearing seemed to be OK, no play or roughness in rotation, so I
decided to leave well alone and concentrate on the obvious faults.
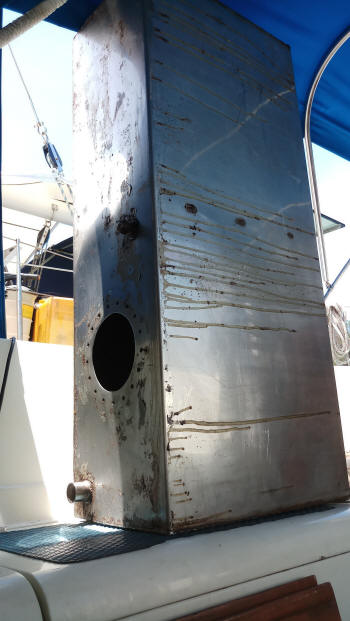
Removing the second gearbox inline, (the transfer or
reduction gearbox) which changes rotary action
into linear proved to be a major challenge. It is deep in the port
cockpit locker at the after end of the fuel tank, beside the calorifier
tank and under the bilge pump! After several days of trying to
remove it from it's bracket, we decided the only way was to first remove
the fuel tank to allow some access. I cut away the fibre glass
that secured the top of the tank, pumped out 120 litres of fuel and then
struggled to get the tank out of the locker - the aperture is just
big enough!
The tank contained a lot of slimy jelly like substance
(not diesel bug) but clear, like the dead jellyfish you might see washed
up on the beach. I suppose that is another problem solved for a
while - at least I will have a clean tank for a few years!
.jpg)
With the fuel tank removed, I was able to then undo the
three bolts that secured the gearbox to it's steel bracket. The
pic shows the box as it came out, the top vertical shaft connects to the
arm which operates the torque tube leading to the rudder quadrant,
The smaller splined shaft at the front is the input shaft from the
bevelhead gearbox under the pedestal. Beneath that is a plastic oil
drain/filler plug and the box is full of heavy duty gear oil.
Turning the input shaft showed quite a bit of stiffness, so I stripped
it down to it's component parts, as in photo below.
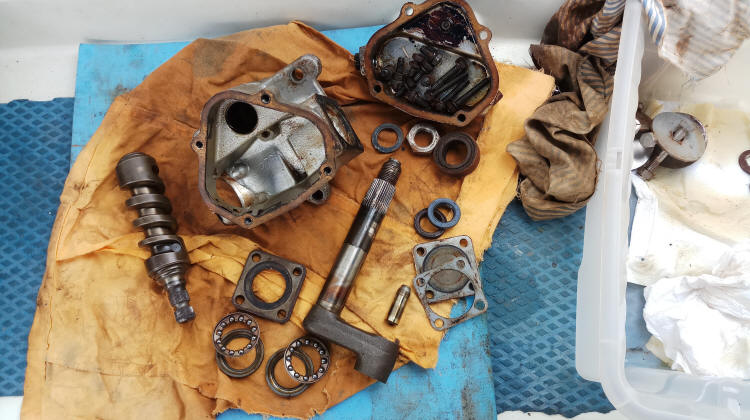
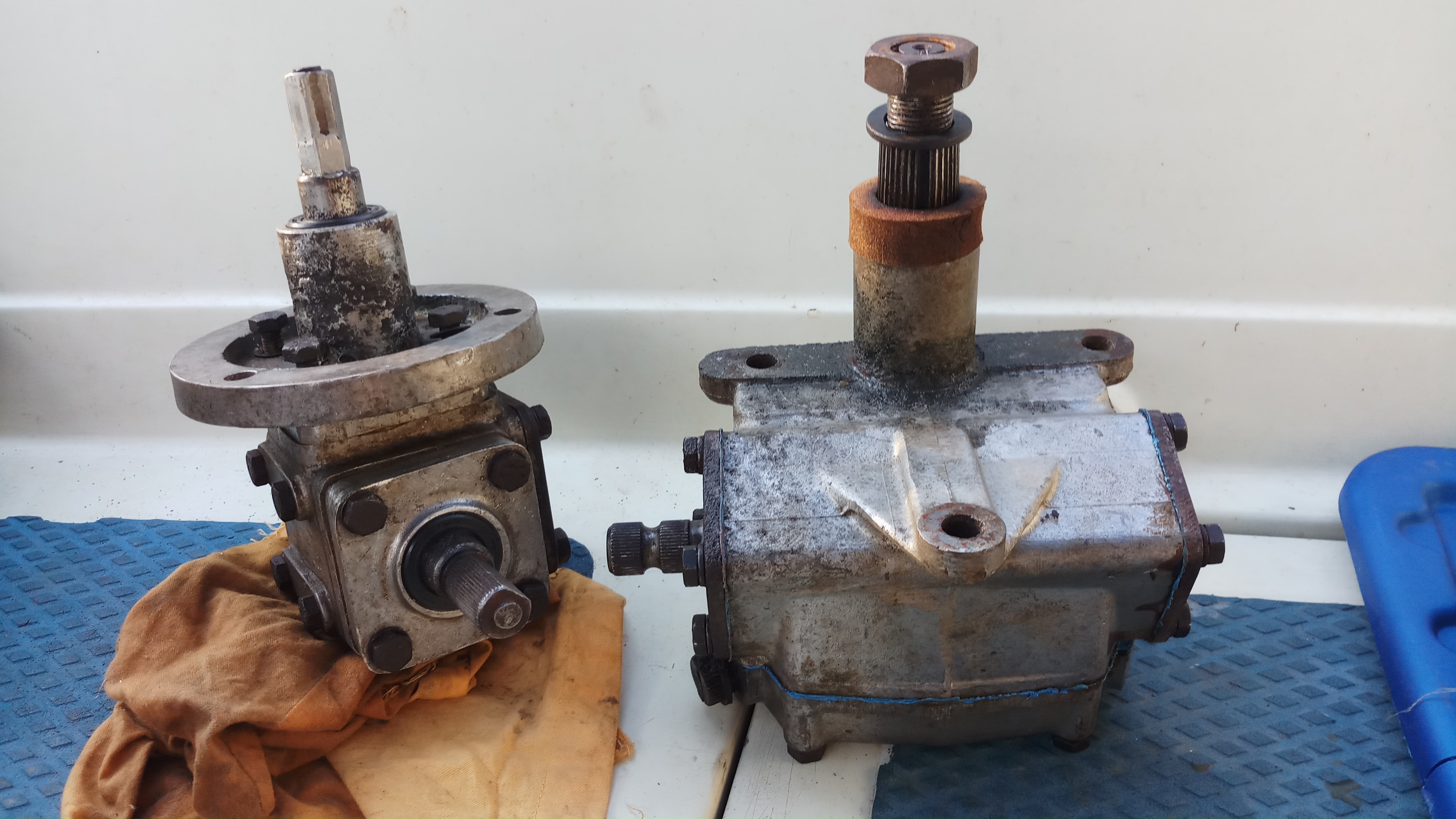
The lower bevel gearbox on the left and the transfer box
on the right, re-assembled and ready to install. The splines on
the input shaft of the bevel gearbox have been ground off and made into
a hexagonal shape. The matching fitting on the pedestal downshaft
has had a box spanner welded into the female splines to fit the
hexagonal shape on the bevel gearbox input. All bearings have been
renewed.
Re-assembly of the whole system was much easier than
taking it apart! With no drawings, I was working in the dark when
removing all the parts, whereas putting it back together was a walk in
the park (almost!)
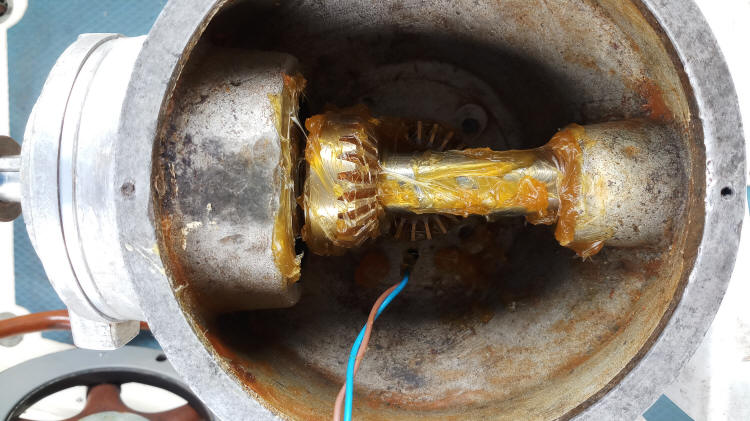
The pedestal bowl re-assembled.
.jpg)
1st bevelhead gearbox installed, along with the torque
tube to the transfer gearbox.
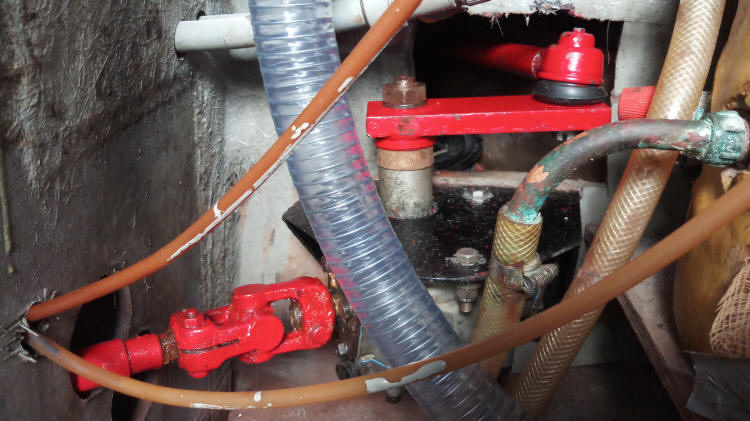
The transfer gearbox installed on it's bracket.
This photo is taken from where the fuel tank would be positioned, so you
can see the confined space in which I had to work. It is
impossible to work on the gearbox with the fuel tank in position.
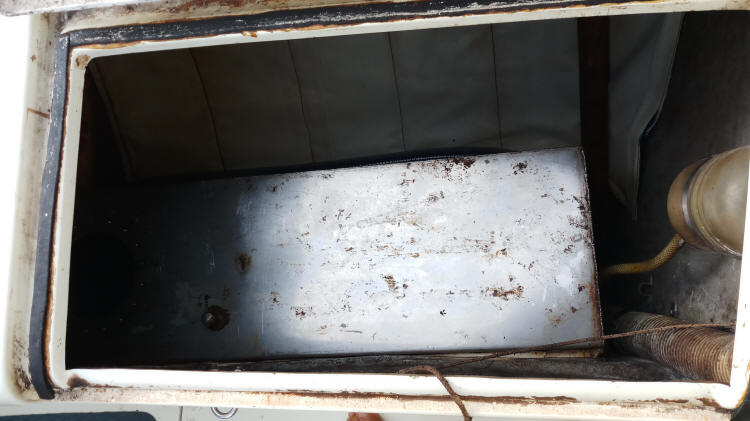
The fuel tank back in the cockpit locker.
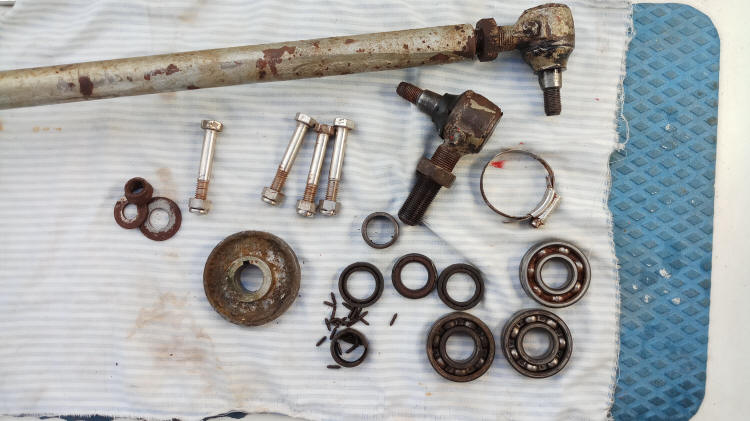
Just a few of the replaced parts.
During this overhaul of the steering, I had considered, priced and
looked at the possibility of taking the whole lot out and replacing it
with a hydraulic system. It would be possible but would entail
doing away with the pedestal and mounting the steering wheel on the
cockpit forward bulkhead, re-siting the engine instrument panel and
making new hatches in the cockpit floor for access to the engine - which
would be good, as it would give access to the shaft and currently
inaccessible stern gland. But......it's not a job I want to take
on at this stage!
The only remaining job to do on the steering now is to 'drop' the
rudder and check the seals/bearings there - which is one of the main
reasons I sailed up to Kudat on this occasion!
More to follow when I haul out.
Due to Covid 19 restrictions and bans on
intercountry/district travel, my haul out is delayed for the foreseeable
future. I see no point in hauling, antifouling and then sitting at
anchor for months, unable to go anywhere, while the bottom fouls up
again!
February 2022
After 19 months at anchor, we finally hauled out and I was able to drop
the rudder for inspection!
Removal was much easier than I imagined it might be.
The boat was positioned so that the keel rested on concrete blocks about
10" high and I needed to dig a hole under the rudder about a foot deep for
the rudder stock to clear the rudder tube.
After placing wooden blocks under the rudder - it
weighs around 60Kg, I removed the two bolts securing the
'shoe' which supports the bottom of the rudder. I had replaced
these two bolts five years ago with ones of 304 stainless steel (all
that was available at the time) and these showed signs of cavity
corrosion on the threaded areas. They are 3/8ths bolts and I am
replacing these with 10mm 316 stainless bolts.
From the aft cabin, I removed the torque bar tie rod
end from the rudder arm (quadrant), loosened the clamp bolt and tapped off the
arm - which really is just a short 1/2" thick steel bar. The
rudder was then free to drop onto the wooden blocks placed below and
gradually lowered out of the rudder tube.
I inspected the rudder stock and was relieved to see
there was no corrosion or cracks visible, which had been a concern of
mine as I have no idea when the rudder was last removed - certainly not
during my ownership.
The top of the rudder tube holds a lipseal to keep sea
water from entering, which is held in place by a circlip. I
removed these for replacement. Inside the tube are two (one at the
bottom, one at the top) plastic/nylon bushes about 2" each in length.
Both seem to be in good condition.
The bottom spigot of the rudder fits in a composite
bush held in place by the rudder shoe, this was showing signs of wear,
so I had another one made.
Refitting was a reversal of the removal and I used a
small hydraulic jack to push the rudder up into place before refitting
the shoe.
