Boat: "Rhumb Do"
Water-maker:
Schenker Smart 30.
Some things on boats are precious, -
fuel, electricity, cooking gas and WATER.
Not all water supplies
can be trusted!
A water maker is
expensive, that's a fact......but they put an end to wondering what sort
of water you are going to get - and how much you are going to get!
Unlike the water
supplies we're used to in the United Kingdom, some countries are decidedly
'behind' when it comes to water purification. We've all heard of
Delhi belly, Karachi crouch and the "don't eat anything that isn't cremated in Egypt,
don't have ice cubes, don't eat salad washed in 'fresh' water."
A water-maker, by and large, removes the worry of rationing your water
supplies, you no longer rely on catching rainwater in your adapted
awnings - and you can basically have a shower whenever you want!
So, I bit the bullet and decided to buy a 'desalination machine' for
Rhumb Do.
There are several makes to choose from and discussions between cruising
yotties about the pro's and con's of each can be heard at the bar on
most nights. I even considered building my own and obtained
plans and instructions to that end. However, time,
difficulty in obtaining suitable high pressure pumps and membrane
housings, plus basic laziness dictated that I buy a commercial unit and
after careful consideration, I opted for the Schenker - not the
cheapest, but reputedly the most efficient with regard power
consumption, a good reputation and the availability of spare parts and
filter cartridges.
At the 2009 London
Boat Show, I purchased the Smart 30 model from Jim of Mactra.
Specifications are an output of 30 litres an hour (probably nearer to
25) and a power consumption of 9amps on a 12volt system. As my fresh water tank is
only 220 litres, and present usage is between 5 and 10 litres a day when at sea, it
should prove ample for my needs and hopefully with the additional solar
panel electrical output, I will only need to run the engine for short periods to
re-charge my batteries.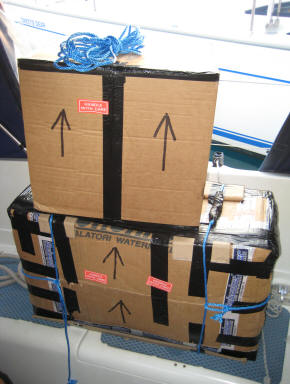
So.....the whole thing was too heavy
and cumbersome to bring back via Thomas Cook from Gatwick to Dalaman
airport and I had to break it down into two boxes for transportation.
Even then, it was a struggle on the inadequate airport trolleys!
Here are the two boxes onboard
Rhumb Do, taking up almost the entire port side cockpit seat while I
pondered the problems of where to fit the various parts within the
limited space onboard.
The membrane, pump, filters (and
water contained within) weigh in excess of 40 kgs and the diesel fuel
tank is situated on the port side (in the locker under the boxes), so I
really wanted to fit the water-maker on the starboard side of the boat
so as not to induce a list to port.
I would have to install the membrane
in the cupboard under the galley sink, and the pump and filters in the
bottom of the forward cabin wardrobe, passing the connecting hoses
through the bulkhead.
The first thing needed was a
schematic drawing of the installation so that I could make my final
plans on the location of each part.
Let's start with the basics.
Seawater contains about 10,500 to 14,000 parts per million (PPM) of
total dissolved solids (TDS), mostly salt (the terms TDS and PPM are
generally used interchangeably). Drinking water has less than 500 TDS.
Water makers make fresh water from saltwater through a process known as
reverse-osmosis desalination. It is really quite a simple process. Sea
water is pumped at high pressure (about 800psi) against a semi
permeable membrane. Some of the water molecules can be forced through
the membrane, while the salt molecules, being larger, cannot. Basically
you're just filtering on a molecular level.
Only about 12-15% of the water passes through the membrane and comes out
as fresh water, so the rest of the water around the membrane becomes
saltier, this water is known as brine water. In order to regulate the
pressure in the membrane and to get rid of the excess brine, some of the
seawater is bled off via a pressure regulation valve. This excess brine
water is discharged overboard. The water that passed through the
membrane is pure, fresh drinking water, usually with less than 300 TDS;
it is referred to as product water and it goes into your tanks (see
above diagram). Pretty simple huh?
In my Navy days, we used steam powered, vacuum controlled evaporators -
basically a large container with a steam coil in the base. The
container was under vacuum (because water boils at a lower temperature
under vacuum) and the sea water was boiled by steam passing through the
coil. The steam created as the sea water boiled was piped away and
condensed into fresh water. Each evaporator produced in excess of
1 ton of pure distilled water per hour.
However, small yachts cannot use that system.......so back to the
fitting of a smaller, different version!
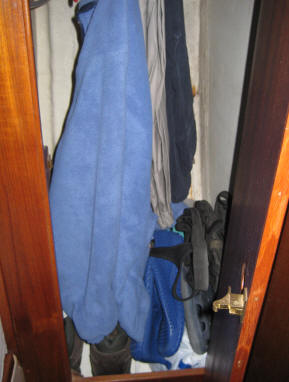
Starting with the pump and filters.
This is the fwd cabin wardrobe where
these were to be sited - the shoes, jackets and trousers would have to
find another home!
On the deck of the cabin, in front of
the wardrobe, is a small hatch giving access to the seacock which
supplies water to the toilet. I would 'T' into this for the pump
suction, bringing the pipe up through the wardrobe floor via a 50 micron
strainer - an item which proved difficult to obtain in Marmaris and had
to be ordered from the UK.
(see updates)
The pipework was easier to run than I
first imagined but the cramped working space was a nightmare - the
wardrobe is only narrow and I needed to squeeze my shoulders through the
door in order to fix the pump base plate, mount the filters and screw up
all the jubilee clips which connect the three way valves needed during
normal use, flushing the system after use and lastly, 'pickling' the
system with chemicals when not in use for some months - such as a lay up
on the hard, or a prolonged stay in a marina.
After a few days of colourful
language and nautical expressions which you will have difficulty finding
in the Oxford English Dictionary, I finally had everything in place. The coiled hose at
the back of the wardrobe is the suction hose used when 'pickling' the
membrane, and will be led to a five gallon drum of chemicals when
needed. The hoses are 16mm internal diameter and all the
connections were double clipped. The 15amp circuit breaker was
made by carefully cutting a hole in a waterproof junction box,
mounting the breaker inside and screwing it to the bulkhead on the right
of these photos. I used 10mm2 marine cable for
both the pos. and neg. feeds to the circuit breaker from the main
panel.
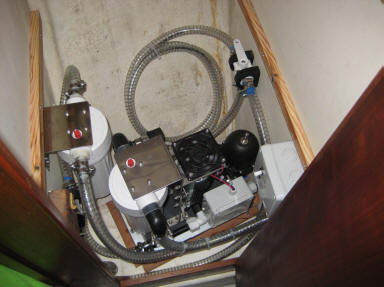
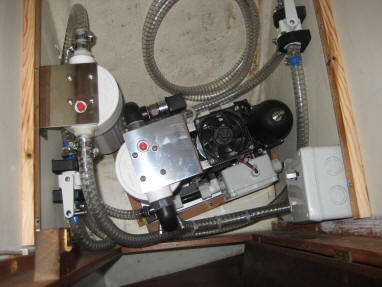
Adding a couple of removable shelves
(10mm plywood) to give
storage space in the top part of the wardrobe finished this part of the
installation - with the exception of cutting ventilation grills into the
door.
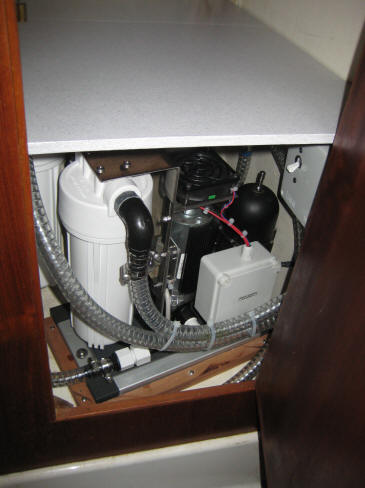
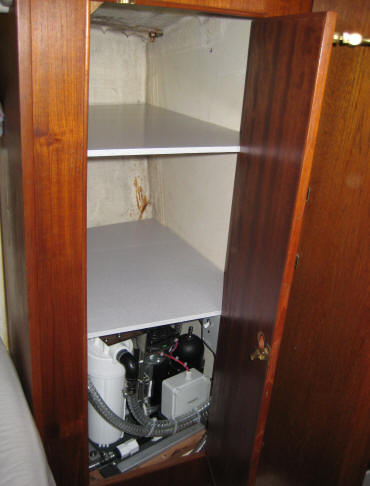
In all the above photographs, one
pipe was for measurement purposes only and was later replaced with high
pressure hose to take water from the 5 micron filter to the
membrane - as below.
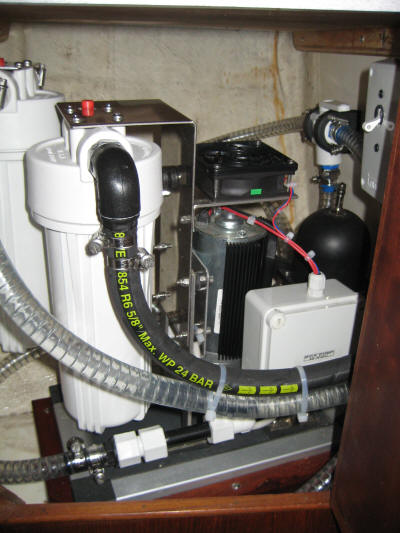
Both filter bodies can be unscrewed
and removed for element replacement despite the deceptive angle of the
above photographs.
Now for the membrane part of it!
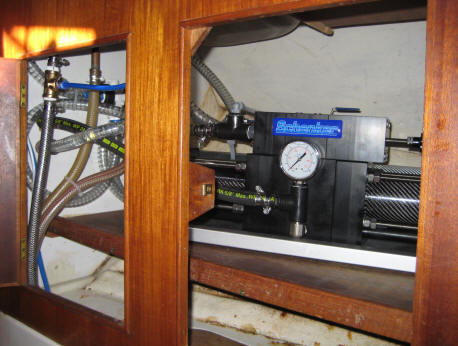
This particular model has to be
mounted in a horizontal position (some types can be mounted vertically),
hence my choice of site - the cupboard under the galley sink.
At first, because the cupboard has two small doors with a 4 inch
vertical piece of wood in between, I thought the whole of the cupboard
front would have to be removed and re-designed, but removing the sink
waste pipe, then tipping the membrane on it's side and wriggling it
around (more naughtical language), allowed me to position the unit on
the shelf and bolt it down.
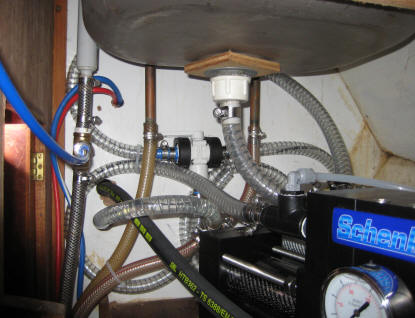
The spaghetti of pipework was then planned out, cut
to length and various sizes of connectors obtained to allow 'T' joins
within the pipes of differing sizes. The new pipework is 16mm
internal diameter, the old is half inch imperial, the sink waste is 19mm
and the 'product water' pipe is 6mm - all had to be joined and include
3-way valves and a non-return valve on the sea water discharge (hidden
behind sink in photo).
Fortunately, replacement of the membrane itself isn't a job that has to
be done every five minutes - more like every five years (with proper
maintenance and flushing) - and it should just entail disconnecting the
pipes to the unit and removing it complete from the cupboard onto a
workbench.
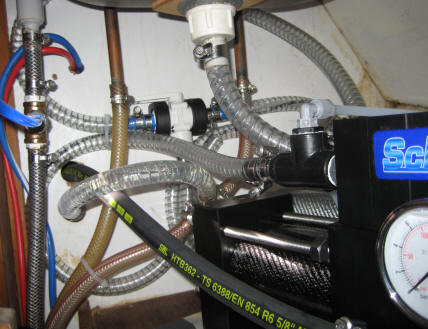
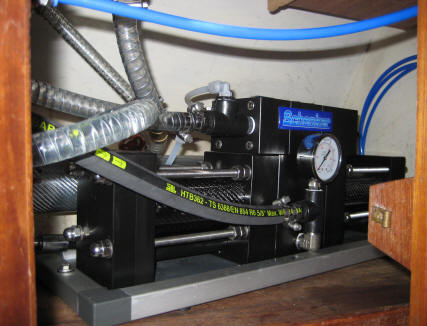
The small diameter (6mm) blue pipe is
the product water pipe, and is plumbed into the sink hand pump supply -
that's because I have a flexible water tank which collapses as it
empties and so requires no breather pipe. For a rigid tank, this
pipe would have to be connected to a quarter inch connector tapped into
the tank top, or into a breather pipe providing the pipe was at least
16mm internal diameter.
The next two jobs were not without
their problems. Firstly, I had to hook up the electrics to the
main panel bus bar - and on my boat, that means taking down the nav.
berth deckhead in order to remove the bulkhead panelling complete with
inverter to get to it. That's a day's work. Secondly,
the raw water pre-pump strainer should have been a straight
forward job of cutting into the heads intake, inserting a t-piece, then
the strainer and connecting to the pump suction pipe......but like all
such 'simple' jobs, it turned into a marathon undertaking.
The installation manual for this
water-maker stipulates that the filter/strainer MUST be one of 50
microns. I was unable to find one! One ordered from the UK
via an on-line catalogue, eventually arrived some weeks later but turned
out to a 50 mesh filter, which equates to around 300 microns.
Following several e-mails to both the chandlery involved and the
supplier of the water-maker, it was decided to fit the 50 mesh filter
which I now had. However.......removing the pipe from the
seacock was impossible and I finally had to cut it off. I now
discovered that the pipe was the approximate imperial equivalent of
19mm, so now I needed a t-piece with two 19mm connectors and one 16mm
connector. Furthermore, the filter connectors were half inch!
The marina chandlery were unable to help and I could not re-connect the
heads intake because the pipe was of an unknown age and had become
hardened and inflexible. A day later, following a search for
suitable connectors and sanitary hose, the water-maker was finally
connected to sea via a complete new heads supply pipe.
(See update 3)
It just remains to cut ventilation
panels into the wardrobe door - and I should be in the water making
business!
I will update this when I have left
Marmaris and am out at anchor - and have tested the installation.
Update 1:
23rd July 2009.......It's now over seven weeks since I left Marmaris Yacht
Marine and I haven't needed to take onboard any water from external
sources during this time. The water maker is working without
problem though I do need to look at the flushing pressure from my fresh
water pump, which doesn't appear to be sufficient. Production of
water is as promised, around 30 litres per hour (well, it filled a litre
bottle in two minutes!) Battery drain is easily covered by the
solar panel - wall to wall sunshine every day - so it hasn't been
necessary to run the engine, although when it is running I
switch on the water maker as needed. Scale in the
kettle is none existent and the water from the tank tastes good - so I'm
well pleased at this moment in time!
Update 2: 29th
January 2010, location - Suakin, Sudan. After six months of
trouble free usage, the unit started to play up on the approach into
Suakin. Whilst in use, the pump suddenly stopped, with the
manometer showing a high pressure of 10 bar. The seas were quite
rough and I at first put the fault down to this, although the unit is
mounted horizontally and longitudinally in the boat, so it shouldn't
really make any difference. However, later at anchor, the fault
persisted despite going through all the maintenance and corrective
issues described in the (poorly written) manual. The pump would
not self-prime when switched to sea water intake and I suspected the 5
micron filter to be a suspect cause as this was renewed in Hurghada,
Egypt - not by the original paper pleated type, but by a sort of
compressed polyester type. After three days of trying to sort the
problem out, and phone calls to the supplier, I replaced the filter with
an original pleated type and although it should not make any
difference, it does!! The unit is now working correctly
again.
Update 3:
1st July 2010.......It became apparent sometime ago, that things were
not as they should be. The watermaker kept cutting out with either
high pressure or (more likely) loss of pressure entirely. Some
other yotties who have the same model have removed the pre-pump strainer
(which the manual insists must be 50 micron) and now run their units
without any initial filtering. Others have advised that the pump
cannot 'suck' through a filter and must in fact 'push' the water through
any restriction. In my case, after much deliberation, I put the
fault down to the shared suction with the heads inlet (a Lavac toilet),
reasoning that the pump suction was taking the easiest route and
emptying the pipe between the t-piece and the heads bowl, thereby
eventually sucking in air instead of water from the seacock. I
disconnected the heads intake and connected the watermaker pump directly
to the seacock - and this cured the problem. A shared intake
pipe may be OK with a Jabsco toilet or some other make, but if you have
a Lavac, then in my opinion you will have to fit a
dedicated seacock for watermaker use only.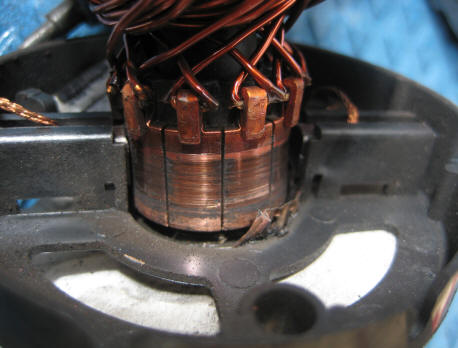
Update 4:
October 2010......unable to use the watermaker in Langkawi because of
dirty anchorage water, I decided to pickle the membrane. However,
the pump again would take a suction and eventually, making a horrible
mechanical noise, ground to a halt. Stripping the unit down
revealed that the motor commutator was totally wrecked by a jammed piece
of brass/copper which appeared to have come from around the top bearing
assembly. Jim MacDonald of Mactra said he had never seen a pump
motor damaged in such a way and kindly sent the photo's to Schenker who
were not very helpful. Jim as usual, was more than considerate and
forwarded me a new motor at cost price.
Update 5:
December 2010.....whilst hauled out of the water in Chebilang, Thailand,
I fitted a dedicated sea water intake valve - something which I advise
as 'essential.' This of course allowed me to reconnect the
heads intake and have a working toilet again!
Back to April 2009 Log
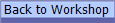
